A Test Stand for Giants
With its avant-garde and flexible all-wheel drive chassis dynamometer for agricultural vehicles, Renk Test System GmbH (RTS) is setting new standards together with AGCO and HELUKABEL.
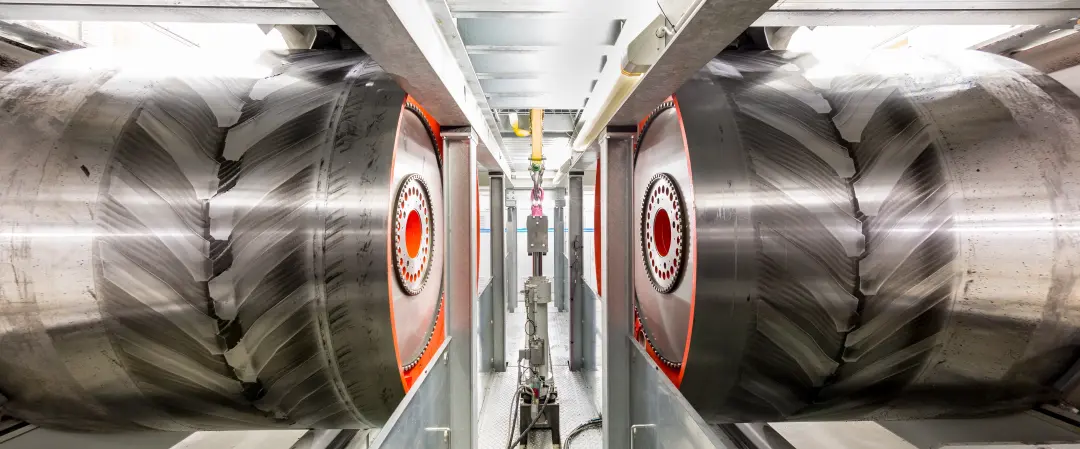
The four giant steel rollers rotate around their own axis, making the enormous heavy tractor placed upon them look as light as a feather: this is the first impression conveyed by the most avant-garde and flexible all-wheel drive chassis dynamometer of its kind. The rollers are driven and braked by the vehicle on the test stand. They simulate the resistance that the vehicle would have to overcome on roads and on other terrain. The project was an ambitious one that took just 14 months to complete. The result was a dynamometer for AGCO, located in its Marktoberdorf plant in Bavaria. For some time, senior leaders at the American agricultural machinery manufacturer had been on the lookout for a custom test stand that would allow for the comprehensive and reproducible testing of its entire AGCO vehicle range on a single piece of equipment.
Previously, testing a tractor, for example, and its attachments under realistic load conditions was a costly and time-consuming business, one which included test drives at home and abroad. In addition, often, individual parts had to be methodically tested and checked at the development stage, before the vehicle had even been constructed. So, AGCO decided to find a way to bring the field into the lab. This was no easy undertaking. As Michael Gramlich, Head of Electrical Design and Safety Engineering at RTS, recalls: “The planning and design requirements for the multifunctional all-wheel drive chassis dynamometer were tough. For example, we needed to be able to position a wide diversity of agricultural vehicle types with varying wheelbases on the chassis dynamometer without lengthy changeover times. We also had to be able to access the vehicle during the testing.”
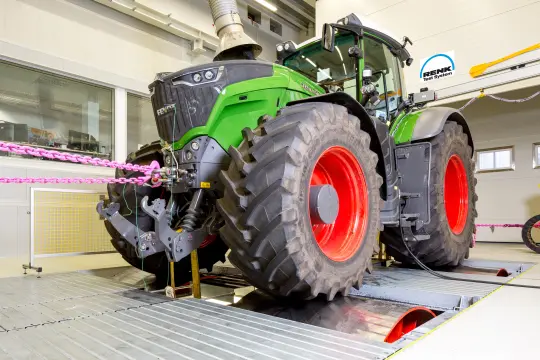
Exceptional Current Carrying Capacity
The structure of the equipment, including its cabling, is extremely robust. After all, enormous torques of up to 80,000 newton metres per wheel are generated when agricultural machinery is tested in continuous operation. Mock-ups of typical tractor work cycles and dynamic driving tests also simulate various uphill and downhill gradients, something which requires an extremely stable design. The decisive factor for the dynamometer’s cabling was high bending flexibility, but even more crucial was high current carrying capacity. Michael Gramlich: “The motors in the equipment work at high torques. There's a lot of power to be transmitted. We therefore installed ten cable strands in each motor, each 60 metres long. But then we had a problem with the heat generated by the cables which were lying on top of each other in the cable duct. This heat caused a drop in power and hence a decrease in the current carrying capacity.” The dynamometer therefore needed a special insulation to cope with the higher temperatures. “And HELUKABEL was able to provide a solution with an exceptional current carrying capacity.”
Small Cross Section – Big Pay-Off
There was another challenge: the different wheelbases of each vehicle type on the dynamometer. Each time the equipment is altered - and that can be up to three times a day - the cables are moved along with the drag chain. This means they must be flexible, just like the dynamometer. Many off-the-shelf cables meet the equipment’s high-power requirements, but their large cross sections mean their bending radii are too big to give the dynamometer the flexibility it needs. “HELUKABEL developed a special cable for us with a reduced cross section and smaller outer diameter which gave us the optimal bending radius,” reports Gramlich, who points out that “you wouldn’t find a cable like that in a catalogue.” The five-millimetre reduction in cross section also had other advantages, as Dominik Riedl, Area Sales Manager at HELUKABEL explains: “Our cable is not only space-saving, it’s also lighter and easier to handle which speeds up installation. All these advantages are due to the cross-linked core insulation which permits higher operating temperatures in the conductor.
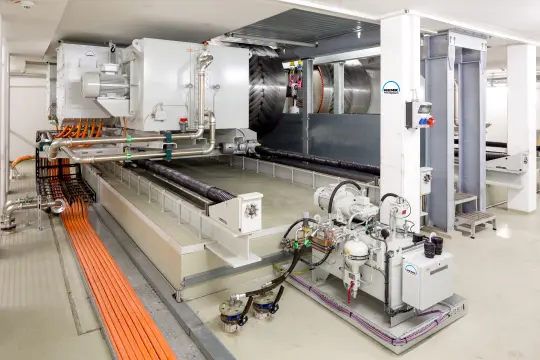
Its robust PUR sheath makes the cable abrasion-resistant and hence ideal for installation in the drag chain. It can also be connected to the motor in next to no time.” All these aspects played a role in the joint planning with partner RTS. The result was the use of one of HELUKABEL’s most efficient, flexible and innovative products: the TOPFLEX® MOTOR EMV 3/3. This two-standard motor power supply cable for frequency converters with triple screening ensures excellent electromagnetic compatibility (EMC) in machinery and equipment and thus meets the required current carrying capacity. “Our TOPFLEX® also distinguishes itself through an earth core cross section divided into thirds and an even distribution of the interstices between the power supply cores,” says Riedl, describing the key features. The 3-core symmetrical structure of the heavy-duty cable greatly improves EMC performance. At frequencies of up to approximately five megahertz and under symmetrical loading, the magnetic fields around the three phase conductors more or less cancel each other out.
Engineering Artwork on Three Floors
In order to fulfil all the chassis dynamometer requirements, there was one question that needed to be answered and that was: what was the drive concept for testing the all-wheel drive giants and hence what spatial dimensions did the RTS team of experts have to think of? Gramlich describes the key technical features of the system: “The test vehicle stands on four independently-operated roller units in the dynamometer. This flexibility allows for the simulation of important typical behaviour of tractor vehicles, such as tilling on wet ground.” The ability to simulate the “ploughing” work cycle under full load and at low driving speed was crucial to the design of the AC engine power with 250 kilowatts per roller unit. “After all, ploughing creates tremendous torques on each wheel. It was important for us to be able to handle and measure them easily.” The RTS experts went to great lengths to reduce the space required for the new dynamometer: They built the equipment at the AGCO plant on three floors. One floor houses almost exclusively the HELUKABEL cables, including the flexible drag chains for the drive technology. The freely accessible “cable floor” makes maintenance work quick and stress-free.
Unique and Future-Oriented
Another highlight is the newly designed ergonomic operator pit, which is approximately one metre in width. It enables direct alterations to be made to the vehicle during testing without the aid of the customary step irons. In almost no time and from inside the pit, two infinitely adjustable hydraulic cylinders can be positioned on the vehicle in order to simulate additional loads of two tonnes on each axle. The roller units themselves are also infinitely adjustable. The two front units can be individually offset by 2,050 to 6,000 millimetres allowing vehicle types of all AGCO brands to be positioned on the rollers without alteration work. The smooth surface furnish of the rollers ensures the best possible grip and low tyre wear during continuous operation. The unique features of the test system could be listed almost indefinitely. In the meantime, the AGCO Corporation's chassis dynamometer is considered the benchmark.
The Testing Champions
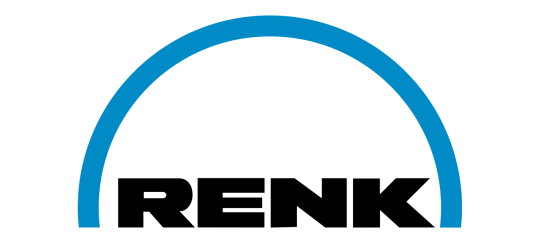
RENK Test System GmbH, based in Augsburg, Bavaria, is one of the leading international suppliers of custom test systems for the development, production and quality assurance of drive technology in almost all applications. The roots of the company, which became an independent entity in 2004, go back to the 1960s.
Find out more about RENK Test System GmbH here: RENK Website
The Flagship
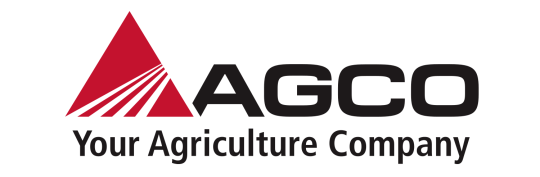
AGCO (Allis-Gleaner Corporation) is one of the world's largest companies in the design, manufacture and sale of agricultural equipment. Through well-known brands such as Challenger®, Fendt®, GSI®, Massey Ferguson® and Valtra®, US-based AGCO provides farmers in more than 140 countries with tractors, combine harvesters, hay and forage machinery, seeding and tillage equipment, grain storage and protein production systems, as well as replacement parts.
Read more about AGCO here: AGCO Website
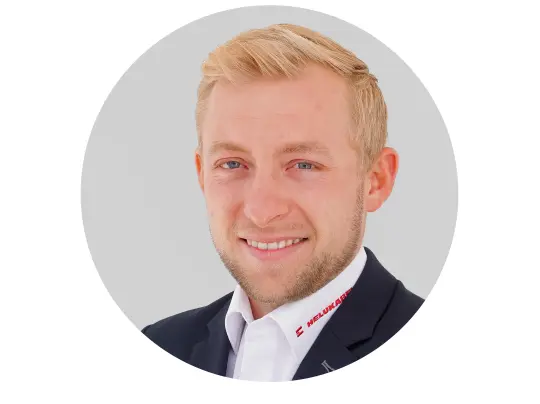
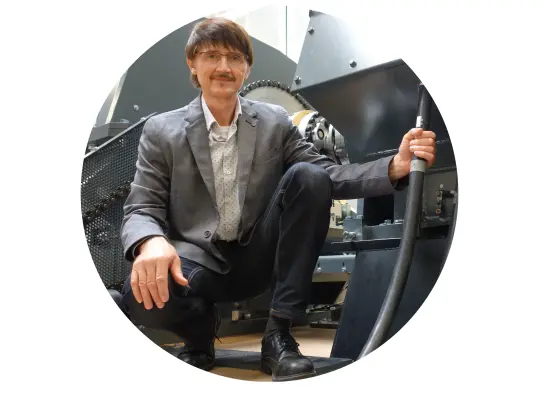